L’impression 3D au service des instruments de musique
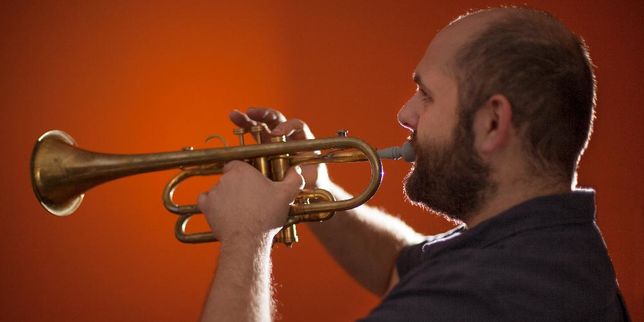
L’impression 3D au service des instruments de musique
Par Nicolas Six
Les imprimantes 3D soufflent un vent d’innovation sur la fabrication d’instruments de musique. Tour d’horizon d’un artisanat inventif, où les Français sont en pointe.
Ce sont des sculptures, imprimées en 3D, autant que des instruments : les guitares électriques d’Odd et de Customuse sont imprimées en Nylon. Le bois est relégué au centre de l’instrument. Leur manche semble flotter au milieu d’un dessin géométrique.
Plus saisissants encore sont les violons électriques du studio Monad. Leur géométrie torturée rappelle les croquis futuristes de l’architecte Zaha Hadid. Certains jugeront ces formes superbes, mais au fond, tout cela est accessoire. En musique, le plaisir des yeux s’efface derrière celui des oreilles.
Ces instruments-là sonnent-ils mieux qu’un instrument traditionnel ? Cela n’est malheureusement pas le cas. Qu’on se rassure, d’autres instruments imprimés en 3D, certes moins spectaculaires, sonnent de bel et bien des façons.
Violon piezoélectrique dessiné par Monad Studio. | ERIC GOLDEMBERG ET VERONICA ZALCBERG AVEC LE LUTHIER SCOTT F. HALL
Un son unique et adaptable pour chaque musicien
Un petit morceau de plastique guère attirant, et qui s’emboîte au sommet des clarinettes et des saxophones, fait aussi des progrès grâce à l’impression 3D. Le bec est la pièce la plus importante de l’instrument, elle change radicalement la couleur du son.
Certains solistes en essaient des dizaines avant de trouver satisfaction. Les plus exigeants font fabriquer un bec sur mesure, et c’est précisément ce que propose la start-up française Shape Your Own Sound grâce à l’impression 3D. « Le musicien peut demander un son plus brillant, ou au contraire plus mat. Il peut obtenir plus de limpidité, ou au contraire plus de souffle. Trois à cinq prototypes sont imprimés, jusqu’à ce que le musicien soit satisfait », résume Pauline Eveno, docteur en acoustique. C’est elle qui conçoit ces becs sur ordinateur, selon les indications des clients, puis les imprime et les expédie par voie postale. Le forfait coûte 300 €.
L'impression 3D au chevet du saxophone
Durée : 03:46
Shape Your Own Sound parviendra-t-il à convaincre tous les clarinettistes et les saxophonistes de s’offrir un bec sur mesure ? Probablement pas : beaucoup trouveront leur bonheur parmi les centaines de becs du commerce. Mais l’impression 3D séduira sans doute les musiciens curieux et exigeants. Tout particulièrement les jazzmen à la recherche « du » son.
L’enfance de l’art
Rien de plus facile que d’imprimer un bec. Une imprimante grand public fait l’affaire. La pièce est si petite qu’elle sort en un seul morceau. Sa forme conique s’imprime sans recourir à des ruses complexes. Mais les becs sont une exception : la plupart des instruments acoustiques sont aujourd’hui difficiles, voire impossibles à imprimer en 3D – la technologie manque encore de précision. Lorsqu’on conçoit un prototype, les pièces les plus délicates sortent de l’imprimante avec des dimensions souvent légèrement différentes de celles souhaitées. Résultat, l’instrument sonne faux, comme ce saxophone imprimé en Nylon.
3D Printed Saxophone - Sneak Preview
Durée : 01:37
La solution ? Réaliser une « V2 » pour corriger les dimensions, parfois même une « V3 ». Exactement comme lorsqu’on fabrique un instrument avec des méthodes traditionnelles. Mais les pièces imprimées présentent un autre souci : leurs surfaces sont irrégulières. On perçoit distinctement les couches d’impression.
Ces défauts forment de très légères turbulences sonores. Certaines pièces doivent donc être poncées. Autre faiblesse des matériaux imprimables, ils sont fragiles, sauf à recourir à des matières hors de prix. Le violoniste Laurent Bernadac l’a appris à ses dépends en mettant au point son violon électrique imprimé en 3D. La tension des cordes était telle qu’il a dû recourir à une imprimante à résine, et déposer un brevet au passage. Résultat, son « 3Dvarius » est facturé bien plus cher qu’il ne l’espérait.
Ces problèmes sont appelés à disparaître à moyen terme. Les prix de l’impression métal ou résine baisseront. La précision des imprimantes 3D progressera. Certains modèles d’imprimante seront même dotés d’une ponceuse automatique. Mais un problème risque fort de perdurer : l’éventail des matériaux disponibles restera pauvre. Impossible par exemple d’imprimer du vrai bois, avec sa texture fibreuse naturelle. Ce végétal est pourtant le matériau de prédilection des instruments à cordes. Ses remarquables propriétés de résonance jouent un rôle central dans la sonorité d’un violoncelle, par exemple.
Pour l’heure, l’impression 3D paraît réservée aux instruments à vent, comme le saxophone ou la clarinette, qui s’accommodent bien de matériaux peu résonnants. Leurs matériaux datent souvent d’un siècle ou deux. Mais la technique peut également servir à fabriquer des instruments acoustiques « électrifiés », comme le violon électrique ou la guitare électrique.
Matériaux innovants
A l’échelle de quelques décennies, parviendra-t-on fabriquer des instruments à corde purement acoustiques ? Pourra-t-on remplacer les matériaux du violon ou de la guitare classique ? Il existe quelques pistes. L’Institut de recherche taïwanais ITRI a fabriqué un saxophone métallique avec une imprimante conçue pour la joaillerie. Son rayon laser modifie la structure moléculaire du métal en temps réel : plus dur ou plus mou.
En France, la start-up Pollen met au point une imprimante capable d’imprimer quatre matériaux en couches mêlées, voire même d’en mélanger deux. S’il devenait possible, dans vingt ans, d’imprimer un matériau résonnant plus que le bois, on pourrait imaginer un violon « amélioré ». Grâce au mélange de plusieurs strates de matériaux, il guiderait les ondes sonores intelligemment. Grâce à une structure interne en nid d’abeille, il modulerait la résonance, en jouant sur la taille des cavités, ou sur leur forme.
Ces innovations ouvrent de nouvelles perspectives aux « facteurs », les fabricants d’instruments. Ceux-ci prennent l’impression 3D au sérieux. La qualité des débats, lors de la journée d’information organisée en mars 2016 par l’Institut européen des métiers de la musique, en atteste. Tout instrument est un compromis technologique qui a vocation à être amélioré. D’autant que l’impression 3D ouvre une autre porte : on peut imprimer des formes nouvelles, impossibles à fabriquer avec des méthodes traditionnelles.
Artisanat high-tech pour formes nouvelles
L’artisan facteur Jérôme Wiss s’est lancé tête baissée dans l’aventure. Son imprimante 3D tourne tous les jours dans son atelier de Compiègne.
« Après avoir fabriqué des embouchures de trompette, je me suis attaqué à l’instrument entier. Je voulais repartir d’une feuille blanche pour imaginer une trompette qui sonne plus juste que celles fabriquées en Asie. »
Le logiciel Resonans a permis à Jérôme Wiss de tester une multitude de trompettes virtuelles, en modifiant les dimensions des pièces en quelques secondes. L’impression 3D lui a permis de réaliser ces pièces extrêmement rapidement. Le prototype final, lui, a été fabriqué traditionnellement.
Jerôme Wiss présente, à gauche, une pièce imprimée en 3D qui a servi à prototyper la trompette finale, à droite. | NICOLAS SIX POUR « LE MONDE »
« J’ignore si mon projet aurait abouti sans ces technologies. J’y aurais probablement passé plus de dix ans, j’aurais dû investir des dizaines de milliers d’euros. Grâce à la modélisation acoustique, grâce à l’impression 3D, j’ai sorti un prototype en moins d’un an pour quelques milliers d’euros. » La trompette de Jérôme Wiss sonne effectivement plus juste que les modèles traditionnels. « J’ai invité une vingtaine de professionnels à l’essayer. Ils la trouvent extrêmement facile à jouer. Sa justesse les trouble un peu. » Depuis leur plus jeune âge, les trompettistes sont en effet habitués à corriger les fausses notes naturelles de leur instrument.
Démocratiser l’innovation
Doit-on s’attendre à un renouveau de l’artisanat local ? Voire à une relocalisation de la production de certains instruments haut de gamme, aujourd’hui fabriqués en Asie ? Ce qui est certain, c’est que l’impression 3D est en train de démocratiser l’expérimentation. Elle pourrait favoriser l’émergence d’instruments radicaux et disruptifs. Les grandes marques d’instruments, elles aussi, commencent à utiliser ces technologies de prototypage. Exemple : le prestigieux facteur Buffet Crampon a recouru à l’impression 3D pour prototyper la clarinette Cagima, conçue par l’Ircam.
Prototype de la Clarinette Cagima (Buffet Crampon, IRCAM, ANR). Chaque trou correspond à un demi-ton.
Mais pour développer un prototype d’instrument acoustique de A à Z, il n’est plus indispensable d’avoir une forte capacité d’investissement. Pour lancer la fabrication d’une petite série d’instruments, il n’est plus obligatoire d’être à la tête d’une usine. A l’avenir, le succès pourrait dépendre de la qualité des idées plus que de la taille de l’entreprise.
Le poids du passé
Reste une question épineuse : les musiciens adopteront-ils ces instruments innovants ? Les musiciens d’orchestre semblent peu réceptifs aux nouveautés radicales. Beaucoup d’orchestres sont tournés vers la musique composée avant-guerre. Cette logique patrimoniale pousse certaines formations à revenir aux instruments anciens, pour se rapprocher des intentions de Bach ou de Beethoven, revenir aux timbres et aux équilibres d’époque, et aux contraintes de jeu d’antan. Dans le domaine des instruments, l’innovation a considérablement ralenti depuis l’époque bouillonnante du XVIIIe et du XIXe siècle. La forme de la clarinette, par exemple, s’est stabilisée fin XIXe. Elle n’a plus beaucoup bougé depuis, comme le montrent les collections du Musée de la musique :
L’évolution des clarinettes. Collections du Musée de la musique, Philharmonie de Paris. | JEAN-CLAUDE BILLING
Dans les conservatoires, qui forment tant de musiciens, le répertoire passé reste privilégié, en dépit des efforts récents pour inviter des compositeurs contemporains. Seul le microcosme du jazz semble vraiment séduit par l’innovation facturale. Plusieurs grands saxophonistes français utilisent les becs imprimés en 3D de Pauline Eveno. Mais que pèse le jazz face aux musiques dites « classiques » ?
Heureusement, les artistes de musique « populaire » s’intéressent aussi à ces innovations. L’impression 3D peut contribuer à alléger certains instruments, voire à améliorer leur confort. C’est l’intérêt principal du violon électrique imaginé par Laurent Bernadac, un jeune violoniste médaillé du conservatoire de Toulouse, par ailleurs ingénieur INSA. Le 3Dvarius pèse 50 grammes de moins qu’un violon électrique Yamaha. Un gain ressenti, puisque les violons sont inconfortables par nature.
« La masse de l’instrument est décentrée pour libérer les mouvements du violoniste. Et il s’adapte à tous types de coussins pour coller à la morphologie de chacun. »
Le violon 3Dvarius dans les mains de son concepteur, Laurent Bernadac, ingénieur, et musicien médaillé du conservatoire de Toulouse en violon Jazz. | THOMAS TETU
Laurent Bernadac a soigné la conception acoustique de l’instrument, imprimé dans une seule pièce de résine, fort complexe, qui laisse les ondes se propager. La commercialisation du 3Dvarius a démarré en juin. « Je suis en capacité de produire 100 violons par an. » A 6 300 €, le 3Dvarius est trois fois plus cher que le meilleur violon électrique Yamaha. Cela n’a pas empêché 144 contributeurs de financer le projet sur KickStarter.